MIM
Online casinos have been increasingly using metal products in their gaming operations. The use of metal products provides online casinos with a number of advantages, including improved security and increased durability. Metal products are often used in online casino gaming tables and chairs. They are also used in the construction of gaming equipment, such as slot machines and roulette wheels. Metal products are highly durable and resistant to wear and tear, making them ideal for use in online casinos. Metal products can also be used to create decorative elements in online casino https://onlinecasinos333.com/. For example, metal letters or symbols can be used to add a touch of elegance to an online casino’s décor. Metal products are also often used in the construction of casino signage. The use of metal products in online casinos provides a number of benefits that improve the gaming experience for both players and operators.
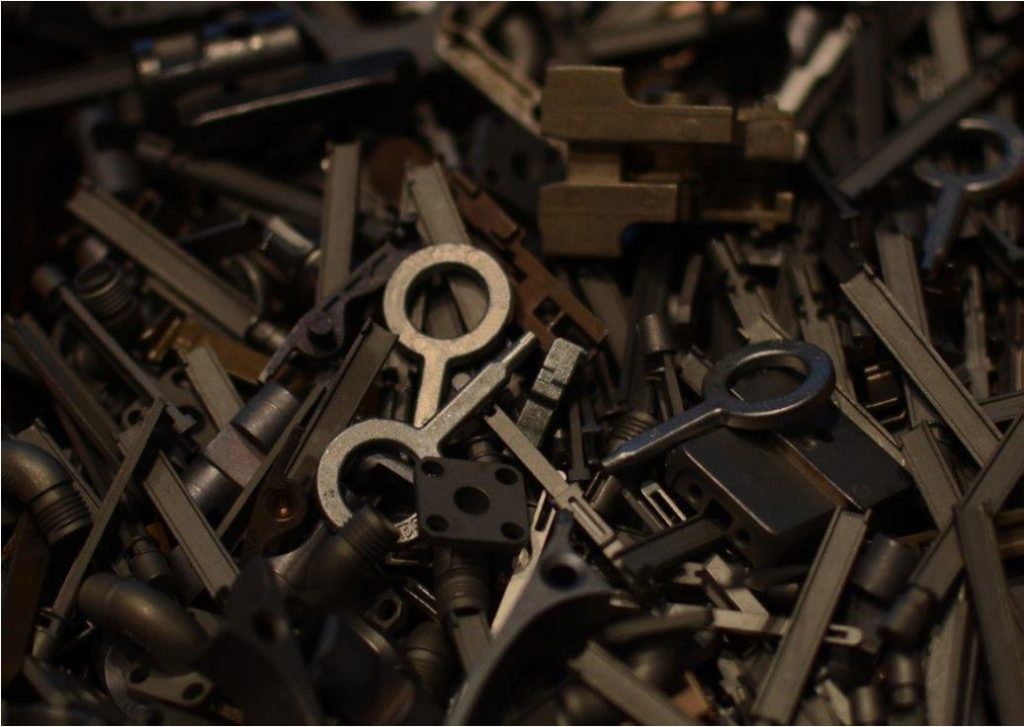
FASTMIM
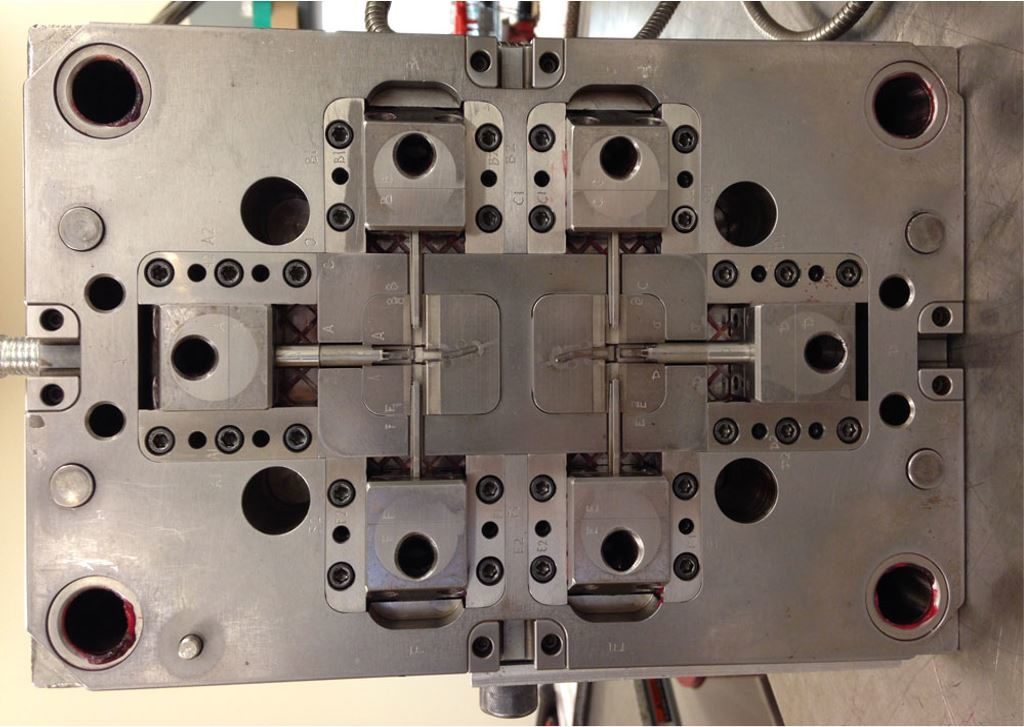
HDMIM
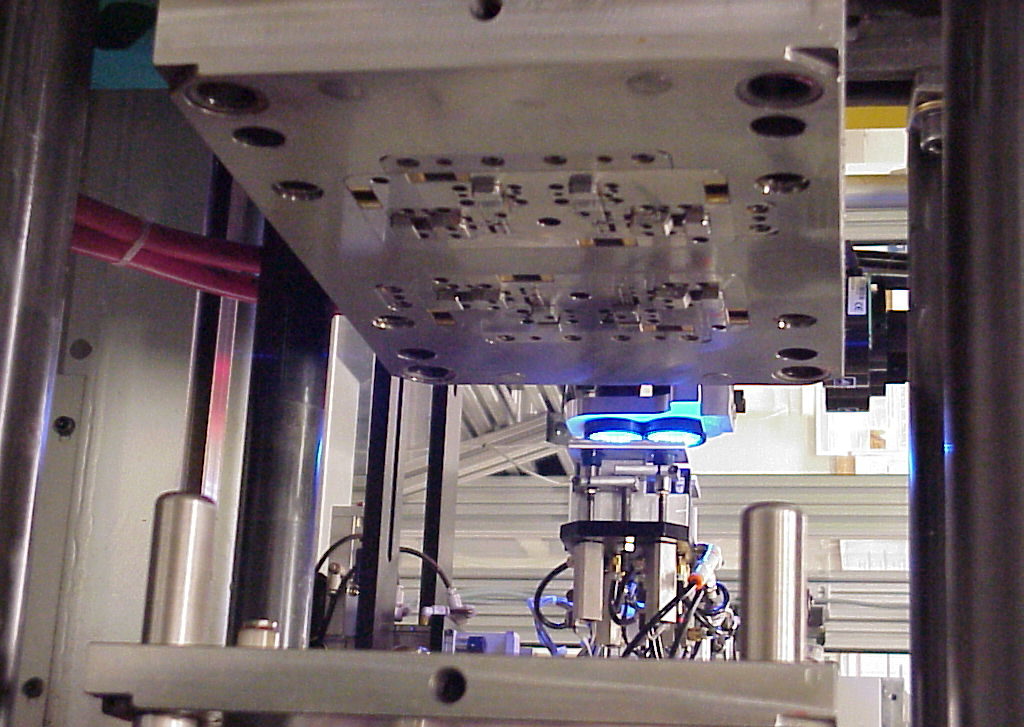